Is Your Workplace Injury Prevention Program Up to Scratch?
Evaluating Your Injury Prevention Program: Key Steps to Align with Australian Standards and Enhance Workplace Safety
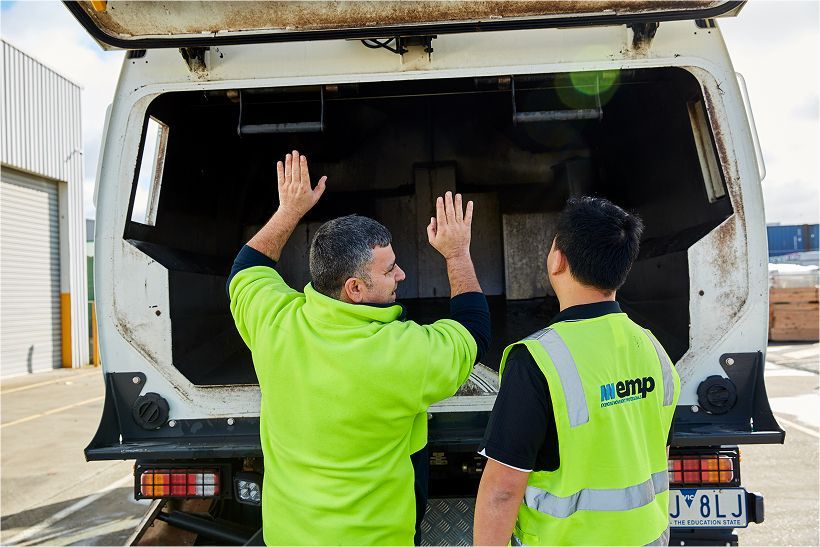
Is Your Workplace Injury Prevention Program Up to Scratch?
Workplace injuries in Australia represent a significant cost to businesses and a burden on the national economy. Safe Work Australia reports consistently high rates of workplace injuries, with physical injury still accounting for the highest number and frequency, translating into billions of dollars in compensation claims and lost productivity annually. The average cost for a physical injury claim in Australia now exceeds $40,000!
Is your workplace injury prevention program able to meet these challenges? Do you even have an injury prevention strategy in place? Where do you start if not?
Failing to implement a robust program can lead to substantial financial impacts, legal repercussions, and damage to your company's reputation. With next year’s budgets starting to be set, there’s no better time to assess whether your current program measures up.
Assessing Your Program. Start by comparing against Australian Standards:
The first step is to evaluate your current injury prevention program against the relevant Australian standards, primarily AS/NZS 4801:2021. This standard outlines the requirements for occupational health and safety management systems. Key areas to consider include:
- Risk Assessment: Do you have a comprehensive system for identifying, assessing, and controlling workplace hazards? This includes regular inspections, hazard identification checklists, and ongoing monitoring of risk levels. Failing to proactively identify and mitigate risks increases the likelihood of injuries and associated costs. This includes risks linked to hazardous manual handling can cause catastrophic and costly injuries.
- Safe Work Procedures: Are there clear, documented procedures in place for all tasks, including detailed instructions for safe work practices? Are these procedures regularly reviewed and updated? We often see outdated procedural guides and processes that have likely contributed to injury. This simple update can be inexpensive and effective in reducing injury.
- Training and Education: Do your employees receive regular and comprehensive training on workplace safety procedures? Is this training tailored to their specific roles and responsibilities? Insufficient training leaves employees vulnerable to injuries. Typical how to lift training is ineffective, thus, a new form of manual handling education is required. We often tailor our interactive training to company need. This is considered best practice.
- Emergency Procedures: Are there well-defined emergency procedures in place, and are all employees adequately trained in their implementation? Having a well-rehearsed emergency response plan is vital for minimizing the consequences of incidents.
- Consultation and Communication: Do you have established channels for consulting with workers on safety matters? Are your safety reps and safety staff visible and known onsite? Effective communication fosters a strong safety culture, promoting employee engagement and participation in preventing accident and injury.
Common Shortcomings and How to Address Them:
Many Australian workplaces fall short in the above areas, including;
- Inadequate risk assessment: Focusing on obvious hazards while overlooking more subtle risks.
- Poorly documented safety procedures: Lack of clarity and consistency in safety instructions.
- Insufficient training: Inadequate training or training that is not regularly updated.
- Poor communication: Lack of engagement with workers in safety matters.
Addressing these shortcomings requires a proactive approach, including regular safety audits, updated risk assessments, and ongoing training programs.
A Self-Assessment Checklist:
To help you assess your injury prevention program, consider the following checklist
- Do I have clear and concise job descriptions, safe operating procedures and job task analysis documentation?
- Do I have an incident notification system, injury reporting system and return to work processes in place?
- Do we have regular data supplied and reviewed to identify trends?
- Are my job description, safe operating procedures and job task analysis documents all up to date?
- Do we offer relevant and regular safety and process training and record employee attendance?
- Do we invest in aids and appliances to manage manual handling risk?
- Do we have an inclusive, collaborative and supportive safety culture?
- Do we offer forums to provide feedback and collaborate on solutions to safety and injury problems?
By honestly answering these questions, you can identify areas needing improvement and implement corrective actions to strengthen your injury prevention strategy or help determine what a successful program might include.
Investing in an injury prevention program is not merely a compliance exercise; it's a strategic investment that protects your employees and your bottom line, building a positive workplace culture. The cost of inaction far outweighs the cost of prevention.